Автоматизированная линия дефектоскопии
-
Автоматизированная линия дефектоскопии НКТ
Предназначена для неразрушающего контроля НКТ с муфтами или без муфт при их ремонте и восстановлении, с сортировкой по группам прочности. Управление производится программируемым командо-контроллером. Требование к качеству контроля согласно ГОСТ 633-80. Также выполняются требования стандарта ISO.
Линия может встраиваться в участки по ремонту НКТ с различными вариантами компоновки оборудования.
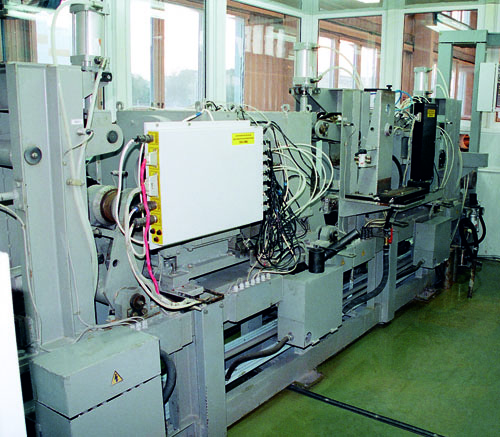
В состав линии входит:
- система комплексного контроля «Уран-2000М»;
- позиция дефектоскопии: электромагнитным-магнитоиндукционным и вихретоковым методом контролируются поперечные и продольные трещины, несплошность тела трубы;
- позиция ультразвуковой толщинометрии стенки трубы: контролируется минимально-допустимая толщина стенки трубы, в том числе от местного износа типа «проточка»;
- позиция определения группы прочности трубы и навинченной муфты: метод контроля - комплексный, основан на обработке информации, полученной при определении химического состава и электромагнитных свойств металла трубы и муфты.
Одновременно производится размагничивание трубы и муфты;
- позиция индикации с монитором;
- транспортная система (в том числе шкаф и пульт управления).
Линия может поставляться без прибора контроля химического состава материала труб и муфт.
Зона контроля:
- по диаметру трубы - 100%;
- по длине - 98% (концевые участки за муфтой длиной около 50 мм не контролируются).
Преимущества:
В автоматическом режиме осуществляется:
- наиболее комплексная дефектоскопия и контроль качества труб и муфт;
- сортировка и подбор по группам прочности НКТ и муфт;
- получение достоверных показателей качества как отечественных, так и импортных НКТ за счет использования в системе контроля прибора для определения химического состава материала;
- определение границ дефектных участков труб с передачей данных на устройство автоматической маркировки и устройство автоматической отрезки забракованных участков;
- передача данных контроля в систему учета, выпуска и паспортизации труб «АСУ-НКТ» для последующей автоматической маркировки и определения дефектных участков труб.
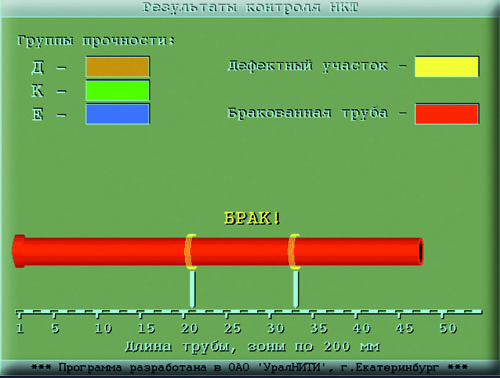
Данные контроля выводятся на монитор
Техническая характеристика:
Производительность линии, труб/час |
до 50 |
Диаметр контролируемых НКТ, мм |
60,3; 73; 89 |
Длина контролируемых НКТ, м |
5,5 ... 11 |
Количество контрольных позиций |
4 |
Скорость перемещения НКТ, м/мин |
20 |
Давление сжатого воздуха в пневмосистеме, МПа |
0,5 - 0,6 |
Суммарная мощность, кВт |
8 |
Габаритные размеры (без транспортной системы и соленоида), мм |
5000 х 1500 х 1500 |
Масса (без транспортной системы), кг |
4500 |
-
Автоматизированная установка дефектоскопии «Уран-3000»
В состав установки входит:
- модуль контроля поперечных дефектов;
- модуль контроля продольных дефектов (роторного типа);
- модуль контроля толщины стенки (роторного типа);
- модуль размагничивания и определение магнитных свойств металла трубы;
- прибор определения химического состава металла трубы типа «Spectrotest»;
- информационно-измерительный комплекс;
- Для контроля продольных и поперечных дефектов используется индукционный метод магнитного контроля
в режиме приложенного поля.
- Для контроля толщины стенки используется ультразвуковой метод
с электромагнитно-акустическим (ЭМА) преобразованием.
- Контролю подвергается вся поверхность трубы,
рабочий зазор между поверхностью трубы и датчиками составляет 0,5…1,0 мм.
- Результаты контроля выводится на дисплеи информационно-измерительного комплекса
и передается в систему АСУ.
Преимущества:
По сравнению с отечественными и зарубежными аналогами:
- высокая достоверность результата за счет использования нескольких взаимодополняющих методов контроля;
- бесконтактный контроль, высокая износостойкость датчиков (ресурс работы не менее 1 года при соблюдении правил эксплуатации);
- высокая чувствительность контроля за счет специальных алгоритмов;
- результат контроля не зависит от наличия на поверхности трубы окалины, грязи и нефтепродуктов.
Установка дефектоскопии поставляется с государственным аттестатом.
Техническая характеристика:
Производительность, ориентировочная в зависимости от диаметра, труб/час |
от 5 до 40 |
Диаметр труб, мм |
от 48 до 426 |
Толщина стенки трубы, мм |
от 4,5 до 16 |
Длина труб, м |
от 5,5 до 13 |
Поступательная скорость перемещения трубы в зоне контроля, м/сек |
до 0,5 |
Потребляемая мощность, ВА |
15000 |
Питание от сети переменного тока: частотой 50 Гц, напряжение 380/220 В |
8 |
Габаритные размеры (ориентировочно), мм |
10000 х 1450 х 2400 |
Масса (ориентировочно), кг |
8500 |
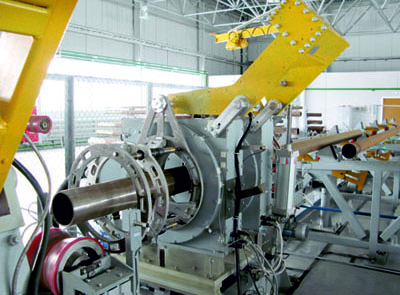 |
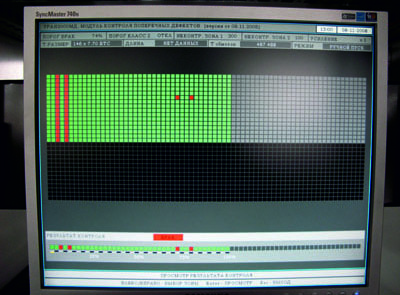 |
Модуль контроля поперечных дефектов |
Результат контроля поперечных дефектов |
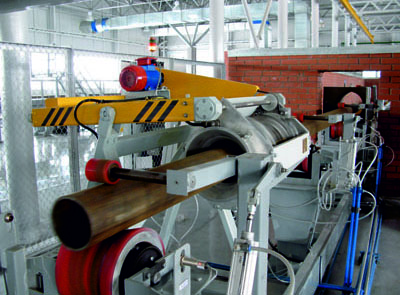 |
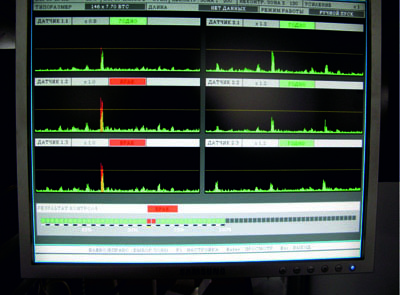 |
Модуль контроля продольных дефектов |
Результат контроля продольных дефектов |
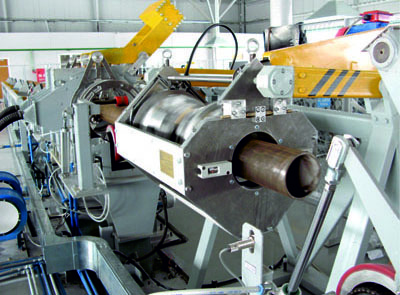 |
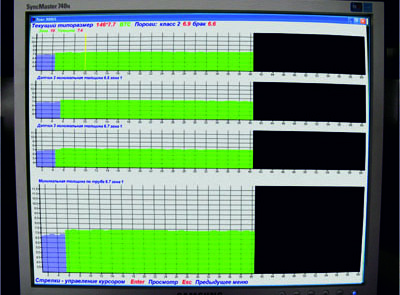 |
Модуль контроля толщины стенки |
Результат контроля толщины стенки |
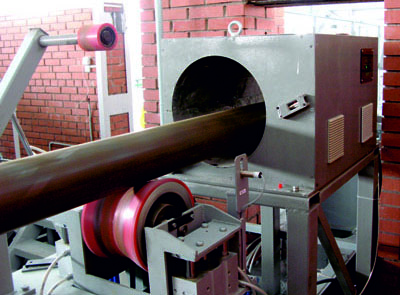 |
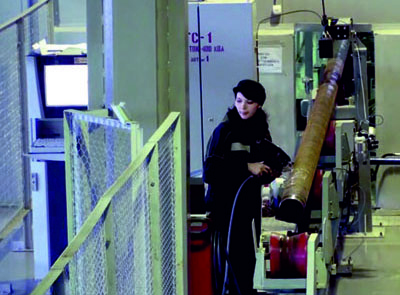 |
Модуль размагничивания и определение магнитных свойств металла трубы |
Определение химического состава металла трубы |
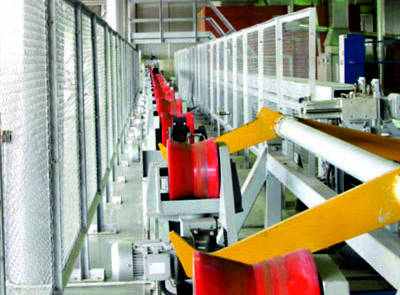 |
 |
|
Информационно-измерительный комплекс |
-
Автоматизированная установка дефектоскопии «Буран-5000»
На основе 10-летнего опыта, накопленного в процессе разработки и внедрении установок дефектоскопии «УРАН - 2000» и «УРАН - 3000», создано оборудование нового поколения «БУРАН-5000». В его конструкции использованы последние достижения в области неразрушающего контроля.
Основные отличительные особенности:
- Использование методов контроля, устойчивых к наличию на поверхности трубы окалины, коррозии, следов грязи и нефтепродуктов, колебанию зазоров между поверхностью датчиков и трубы;
- Использование сканирующих устройств, исключающих разрушение блоков датчиков при контроле труб, имеющих на поверхности задиры и вырывы металла;
- Наличие функции контроля качества сварных швов;
- Повышенные скорости перемещения труб при сохранении качества контроля (до 0,6-0,7 м/с) и увеличение производительности в 1,5-2,0 раза по сравнению с установками типа «УРАН – 3000»;
- Наличие системы самотестирования и проверки работоспособности датчиков, работающей в режиме постоянного мониторинга с выдачей результатов диагностики.
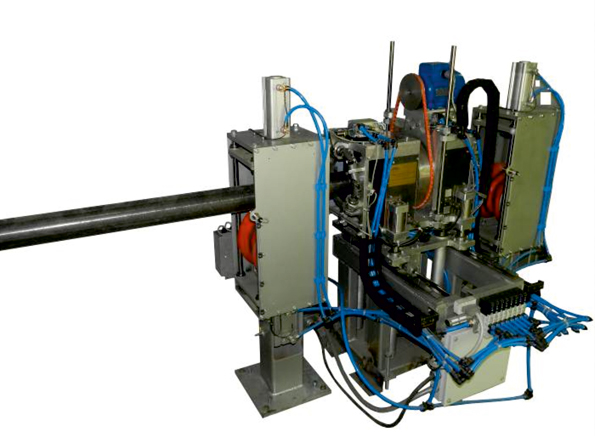 |
Общий вид сканирующего устройства модуля
«БУРАН–5003» для контроля продольных дефектов в работе |